While working on the TDI install retrospectives, it occurred to me that I did not have visibility into the oil system. It bothered me that I did not even have an idiot light to tell me my oil pressure was too low. So, I started working through how I could solve. Today's post starts us on that journey. I started this before the winter holidays, but I'm only really getting down to it now. I had a significant Paulie Axiom event this past week that reminded me of
this old post. The Axiom still holds true; I have new examples almost every week.
Sensing
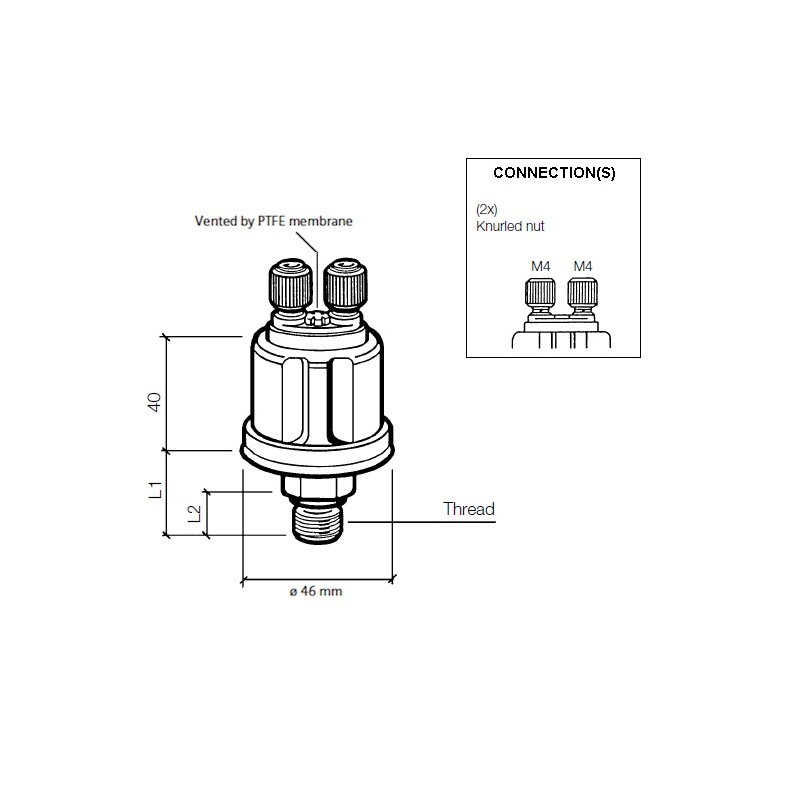 |
VDO 360 006 |
It starts with collecting the oil temperature and pressure information. As I mentioned in the final retrospective (See
TDI Install Retrospective: ECU Dashpod and Sensors), the pressure sensor in the oil filter housing does not send an "honest" pressure. It somehow sends a relative pressure, so you can't just tie into it for a gauge. I don't want the ECU to freak out because there isn't a pressure signal either, so we need to find a good spot. Our friends on TDIClub (RacerTodd, specifically, on
this thread) have located a good spot for collecting the oil pressure and temperature from the oil filter housing. In the picture at the bottom, nicked from that thread, the yellow circle is the spot. The thread size, according to him, is M10x1, which aligns with the thread size/pitch of a standard VDO sensor.
So, with this information, I collected (in late Fall, 2019):
VDO 360 006: oil pressure sensor with the dual idiot light (7psi trigger) and gauge posts,
VDO 323 423: temperature sensor (300*F/150*C Max),
VDO 323 088: temperature sensor (250*F/120*C Max) and
VDO 240 850: sensor splitter / adapter so 2 sensors can run out of one spot
I am concerned that I need an adapter because the temperature probes are so long that it would bump up against something inside the oil filter housing. We'll see. Just in case, I had a sensor that was 1/8npt thread so maybe I can figure out an adapter instead. I also got a shorter sensor that tops-out at 250*F/120*C. I'll get to the sensor stuff later.
Wiring
 |
note unused spot to right of speedo
AND a gauge where your right
knee would be. Huh? |
I had intended to run one thick cable from stem to stern for all of my not-typical-bus wiring. Then I considered each circuit individually. This led me to a different decision: 2 thinner cables. Here's why: In the ECU Dashpod, etc posting I linked above, I listed out a number of circuits. Many of these wires run from behind the dashboard (or at the foot pedal) to the spare tire well at the very rear on the driver side. When I add in the desire for idiot lights and a couple of gauges, the number of circuits grew by 5 or 6, but none of them went to the spare tire well. They all ended in the engine compartment where the sensors were. So, rather than plan for a thick cable of, say, 20 wires, I can split that effort into 2. First I will focus on the 6-wire cable that will deliver the signals for the oil temp gauge, the oil pressure gauge and the oil pressure idiot light. Eventually, it will also deliver an Alt idiot light and a low-water idiot light. I'll leave the last wire open so I have it available for something I haven't thought of yet. I'll post on the snaking of that cable after it's done. Depending on the weather, maybe that'll happen soon... or in mid-July. Love those wet Oregon springs.
Gauge(s)
Last consideration is the gauge or gauges. With VDO sensors, VDO gauges are the logical choice. Buses delivered with VDO stuff, so this is staying consistent with original intent as well. Most bay window buses have a blank spot on the dash to the right of the speedometer. Some folks have retrofit a clock or a tachometer in there. Mine is the standard blank plate held on with 2 8mm screws from behind. The visible space within this hole is about 80mm in diameter. A typical VDO gauge is 2-1/16" (52mm). Simple math says that 2 52mm diameter gauges cannot fit into a single 80mm hole. So, I thought about how I could get creative.
 |
which one is the altimeter? |
Creative idea 1 - have the lower half of one of the gauges hidden under the bottom of the ring. This sounds great in theory, but the 8mm screws which hold things to the back of the dash are located at 12 o'clock and 6 o'clock. The 6 o'clock one would prevent any gauge from hanging below like that. I considered setting it off to one side that way, but in order for the housing of the gauge to clear the screw, it would be oriented at 4:30 or 7:30 and look real janky. Plus, the upper gauge would be pushed so far up, the top edge of that gauge would not be visible. So... idea FAIL
Creative idea 2 - get one of those 2-gauge housing things and set it on top of the dash. Okay, this isn't terribly creative. Quite the contrary, this is the obvious idea, but to me it looks so bad. Just look at the picture above. I mean no offense, but the aesthetic just isn't there for me. Currently, my dash top is clear. If I were to add one of those, it would meet the need, but I think the looks would bug me every time I got behind the wheel. Beauty is in the eye of the beholder...
 |
classic 2 gauge housing |
Creative idea 3 - get one of those 2-gauge housing things and attach it to the lower front of the dash facing up. To give you a better idea, consider that when sitting in the driver seat if you were to look down at the steering wheel and look through it, you would be looking at a warning sticker attached to the steering wheel support. If a gauge housing were placed there, it would be relatively easy to mount, easy to see and it wouldn't get in the way of driving nor your legs, unlike the first dash picture where the gauge is right where your right knee would be. This was the leading candidate until I had creative ideas 5 and 6.
Creative idea 4 - get one of those 2-gauge housing things and attach it to the shelf up where everyone else has sun visors. The problem with this one is that the space between the shelf and the ceiling is too short to fit a housing, so it would have to be attached with just a simple ring-mount. They are not pretty, but would work. I would also have to route the signal wires plus the illumination power up there from somewhere. The extra wiring would prove difficult to hide, further detracting from the aesthetic.
 |
part number 911.641.103.x |
Creative idea 5 - get a Porsche combo gauge and fit that into the spare hole. "What's that," you ask. Porsche has VDO gauges stock just like the bus does. They have a 100mm diameter dual gauge that has the oil temp and pressure as well as integrated idiot lights for the alt/generator, and oil pressure. Some of them also included a brake warning light. These run for over $125US on eBay. The biggest problem with this idea is the overall size. If the gauge is 100mm but the hole is only 80mm, then we lose 0.4" in radius, which may effectively block the visibility of the outer edges of the gauges, just like in creative idea 1. There exists an 80mm version of this combo gauge, but I have been unable to find it used, and new it is, like, $325US (well, it
is a Porsche part), so that's not going to happen. I don't think this size was produced for many models nor years.
Creative idea 6 - get the participant bits of a Porsche combo gauge and make your own. This sounds a little nutty, but hear me out. If all I need are the 2 small gauge bits, and I can eliminate the extra space between and around the 2 gauges, perhaps I can assemble a combo gauge that fits. I don't know about idiot lights, but first things first, can just the 2 gauge pieces fit? I mean, somehow the Porsche and VDO people figured out how to make one fit into 80mm, and I sincerely doubt they made special one-use gauge innards to fit that slightly smaller footprint. Considering what
this guy did, my idea is not that far-fetched. He built his own multi-gauge from the working innards of off-the-shelf VDO gauges. Very cool.
---
 |
nicked from TDIClub |
If you've read this blog for any length of time, you know I have to try ideas 5 or 6. Could it be more expensive and ultimately look worse than any of the other options? Absolutely. Could it possibly not even work, forcing me to do one of the other options? Most definitely. But it is this kind of thinking that got the TDI engine into the bus in the first place. So many people said
that couldn't be done, or it was a bad idea or that the engine couldn't withstand running at whatever RPM or putting a water-cooled engine into an air-cooled bus was blasphemy. I was even told to sell my bus to someone who would appreciate it and go buy a mini-van or a Sprinter. blah, blah, blah.
So, while we were
just learning about some new virus discovery in China (
not a dog whistle, just saying that as a reference to a point in time) and a possible first case in the US, I bought one of these Porsche combination gauges off of the UK eBay site for less than $125US delivered. I will see how it looks in the blank spot before I start removing the individual gauges and update as I go. Unfortunately, the VDO folks don't know much about their old no-longer-available gauge components like these, especially when they were built specifically for a car manufacturer. I direct messaged with their staff, and that was fruitless. So, while the old Porsche/VDO combo gauge may look the best, supporting it long-term will be difficult. Ultimately, I may either have to go with one of the other options or build my own out of widely-available VDO gauges that I tear apart like
that 914world poster did. I have both an oil temp and an oil pressure from VDO sitting in my garage from back when I had the original engine, so going that direction would kind of be free. Just time consuming. Here's a
PDF describing a few gauge-cracking methods if you want to give it a try yourself.
Thanks for following along, and if you have any suggestions for other ideas, or opinions on the ideas I've floated, I am absolutely open to hearing them. I just have to try idea 5 first.